Cold Spray Technology for Offshore Maintenance with Woodside
In 2023, Woodside Energy initiated a project to explore the potential of cold spray technology for offshore asset maintenance. Cold spray, a cutting-edge technique where metal particles are accelerated to high velocities and plastically deform upon substrate contact, forms robust metallic coatings without the need for a heat source. This approach eliminates ignition risks, making it ideal for applications in environments like offshore rigs where such hazards are a significant concern.
Unlike traditional thermal spraying methods, cold spray requires no bulky equipment and can now be applied with a small handheld system operated by a single technician on-site. This flexibility aligns perfectly with the demands of maintaining Woodside’s extensive offshore assets, where mobility and safety are critical.
This innovative technology promises significant improvements in asset integrity management. By restoring or replacing damaged coatings with superior cold spray applications, the project aims to extend the lifespan of critical equipment. The initial deployment will target crane booms, where cold spray aluminium coatings will replace prematurely failed liquid coatings, reinstating the protective layer previously removed for non-destructive testing.
The project involved collaboration with Final Year Project student Riley Anstee and research fellow Victor Cruz De Faria, supported by Woodside’s corrosion and coating experts—Mike Brameld, Travis Baensch, and Alistair Lees. A series of qualification tests were conducted to evaluate the mechanical and electrochemical performance of cold spray coatings, focusing on adhesion strength and corrosion resistance. Following successful testing and a demonstration in Perth in late 2023, plans for full deployment in 2024 are underway, with the first application on offshore crane booms.
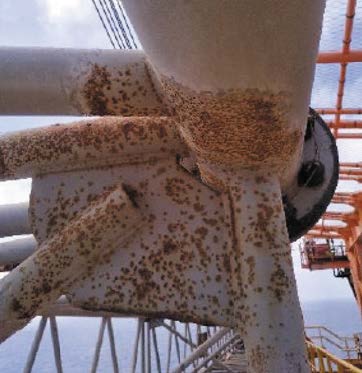
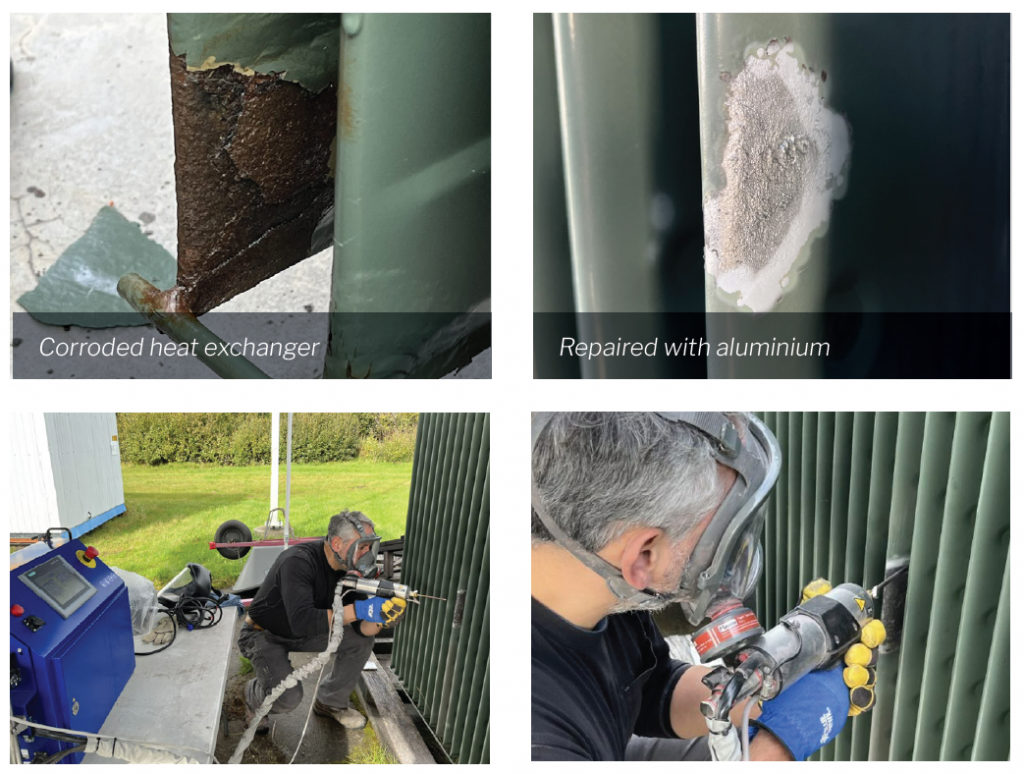
Why Use Cold Spray in Offshore Maintenance?
Offshore environments are among the harshest conditions for structural materials, characterised by constant exposure to saltwater, high humidity, and mechanical stress. Traditional methods, such as epoxies and thermal sprays, often fall short due to delamination, corrosion, and wear over time. Cold spray technology directly addresses these challenges, offering a robust and long-lasting solution for the offshore industry.
Here’s why cold spray is ideal for offshore maintenance:
- Corrosion Resistance Cold spray forms a metallurgical bond with the substrate, preventing moisture and salt ingress that typically cause corrosion. This is a significant improvement over epoxy coatings, which often degrade under prolonged exposure to seawater.
- Geometry Restoration Offshore structures frequently suffer from erosion and material loss. Cold spray enables the precise restoration of damaged parts to their original geometry, reducing the need for costly replacements.
- Minimised Downtime The speed and simplicity of the cold spray process reduce repair times, ensuring that offshore operations can resume quickly.
- Compatibility with Offshore Materials Cold spray supports a wide range of materials, including stainless steel, titanium, and aluminium—metals commonly used in offshore equipment.
- Environmental Sustainability With no need for harsh chemicals or solvents, cold spray is an eco-friendly alternative to epoxies and other coatings traditionally used in offshore maintenance.
- Safety Benefits The absence of red-hot work permits and explosion risks associated with high-temperature thermal sprays make cold spray an inherently safer option for offshore repairs.
Benefits of Cold Spray Over Epoxies and Thermal Spray
- Superior Coating LifespanCold spray coatings exhibit remarkable durability due to the use of metal-based materials and their inherent cathodic protection. Unlike epoxies, which are susceptible to degradation over time, cold spray forms a robust oxide layer that prolongs the life of offshore components.
- Enhanced Mechanical Strength and Abrasion ResistanceThe cold spray process imparts superior hardness and toughness to the coated surface, making it ideal for areas subject to abrasion and impact. Epoxies, in contrast, lack this mechanical resilience.
- Minimal Surface PreparationCold spray requires less stringent surface preparation compared to epoxies and thermal spray, simplifying the application process and reducing time in repair scenarios.
- Geometry RestorationCold spray’s unique ability to rebuild corroded parts to their original dimensions is a game-changer for offshore maintenance. This capability ensures long-term functionality without the need for extensive replacements, unlike epoxies, which merely serve as a superficial layer.
- Material CompatibilityCold spray supports a wide range of metals and alloys, allowing like-for-like repairs and compatibility with existing materials. Epoxies are limited to surface adhesion and often mismatch the base material properties.
- Superior Bond Strength and Corrosion ResistanceThe metallurgical bond created by cold spray eliminates under-surface corrosion pathways, a common issue with epoxies that tend to delaminate over time.
- Environmentally FriendlyBy eliminating the need for harsh solvents and chemicals, cold spray technology aligns with sustainability goals. This stands in contrast to epoxies, which involve environmentally harmful substances.
- Machinability and WeldabilityCold spray coatings can be machined and welded, enhancing their utility in repair applications. Epoxies lack this versatility, limiting their adaptability in complex offshore repairs.
What is cold spray?
Cold spray is an advanced additive manufacturing technology that coats surfaces with strong layers of specialty metals – without ever melting them. In short, fine metal powder is acelerated to supersonic speed, and once these powders collide with the surface, they deform and mechanically bond together to form dense, strong layers of metal.
Want the full explanation on cold spray? Read further on how it works and comparisons between similar technologies.
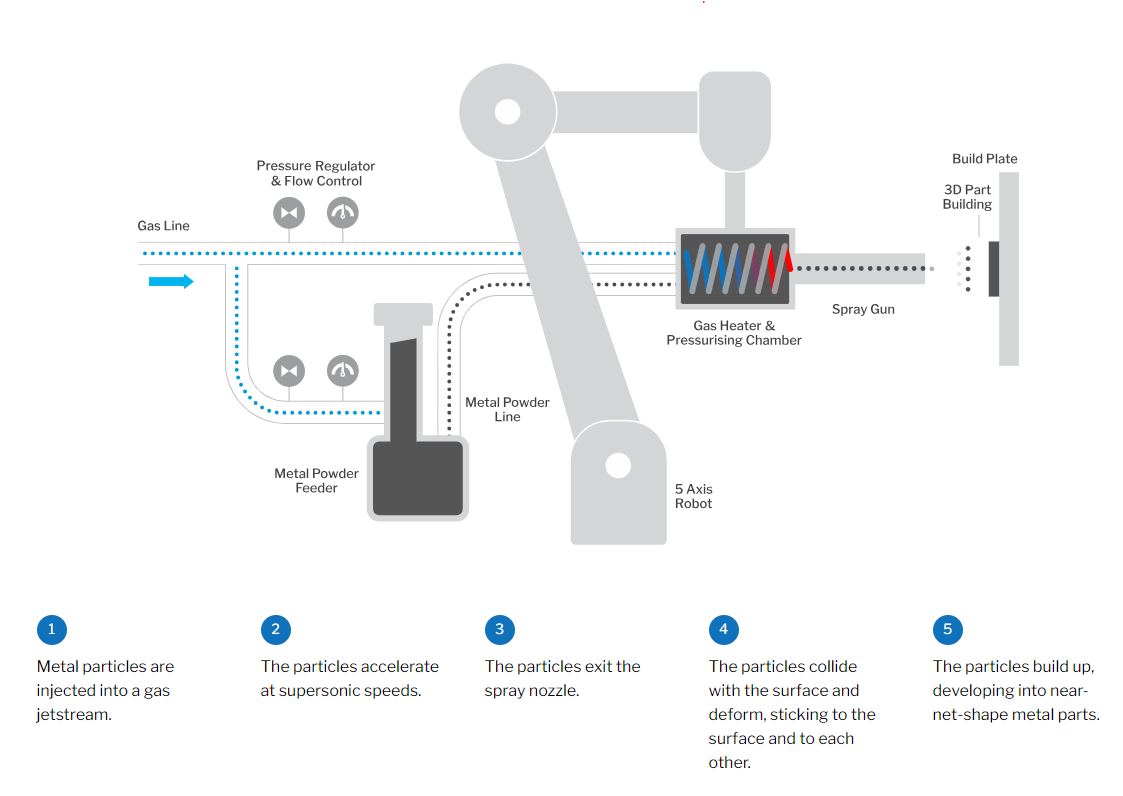