Titomic and nuForj Announce Strategic Partnership to Accelerate Advanced Manufacturing Innovation
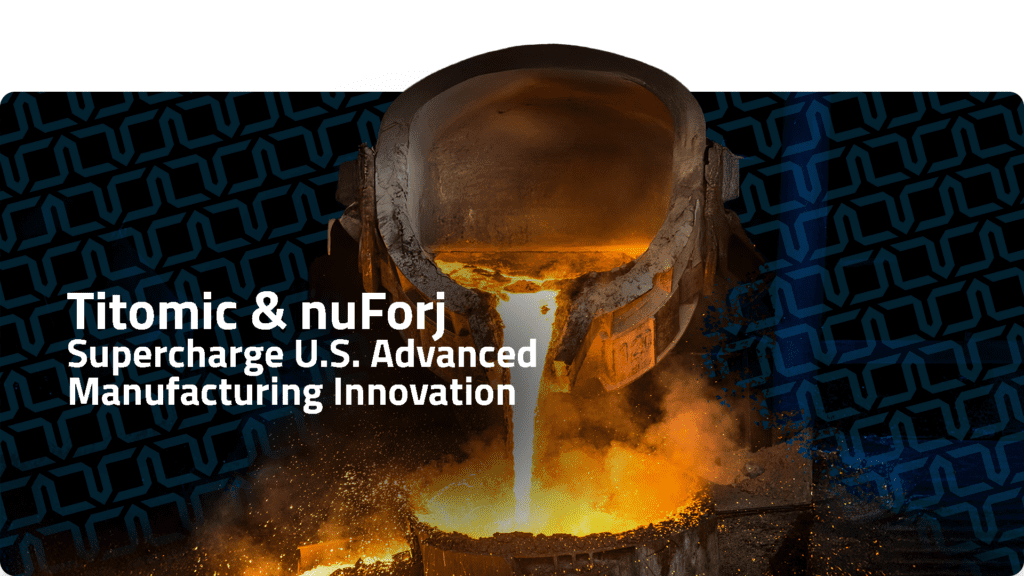
Huntsville, AL – Titomic Limited (ASX: TTT), a global leader in Titomic Kinetic Fusion™, a cold spray additive manufacturing technology, is pleased to announce a strategic partnership with nuForj, LLC, a U.S. based advanced manufacturing service provider, to accelerate commercialization of Titomic’s technology.
Under the partnership, the parties will combine Titomic’s proprietary Titomic Kinetic Fusion™ technology with nuForj’s Industry 4.0 expertise and market reach in the U.S. to provide tailored additive manufacturing solutions for aerospace, defense, education, and industrial sectors. The partnership will also seek to educate and train engineering students about cold spray technology and its application in future industry applications.
“This partnership represents a leap forward in our global strategy. Working alongside nuForj allows us to bring TKF™ technology to critical U.S. markets with agility and deep local insight.”
Jim Simpson, CEO and Managing Director of Titomic
Under the agreement, nuForj will serve as a regional technology and commercialization partner, focusing on delivering tailored solutions to meet the growing demand for repair, coating, and component production using cold spray-based methods.
“The collaboration also paves the way for joint R&D initiatives and the deployment of advanced manufacturing hubs across North America.”
Dr. Patti Dare, President of Titomic USA
“We believe Industry 4.0 technologies and digital transformation of the factory floor are essential to reindustrializing the U.S., powering new business models and driving productivity growth. Titomic Kinetic Fusion™ is an impressive technology for producing quality metal parts incredibly fast and efficiently, and we’re looking forward to making it accessible to scores of companies across the country committed to American manufacturing.”
Rudy Vogel, Founder and CEO of nuForj
This partnership commits both companies to advancing sustainable manufacturing practices, reducing material waste, and enabling near-net-shape production capabilities at industrial scale.
INVESTOR CONTACT
Geoff Hollis
Titomic
Chief Financial Officer
P: +61 438 168 008
E: [email protected]
MEDIA ENQUIRIES
Dr. Patti Dare
Titomic
President, USA
P:+1 408 306 4975
E: [email protected]
Titomic Limited (ASX: TTT) is a publicly listed Australian company at the forefront of industrial-scale metal additive manufacturing. Leveraging its proprietary Titomic Kinetic Fusion™ (TKF) technology, Titomic delivers advanced integrated solutions for OEM production, coatings, repairs, and R&D across global sectors including but not limited to Aerospace, Defense, Shipbuilding, Oil & Gas, Mining, and Automotive. TKF™ enables high performance cold spray additive manufacturing without melting metal powders, making it ideal for manufacturing parts, applying wear and corrosion resistant coatings, radiation protection, and performing structural repairs on-site or in-situ. With its headquarters in Melbourne, Titomic supports its global customer base through regional operations in the USA and Europe, offering comprehensive sales, service, and technical support for its cold spray additive manufacturing technologies. Titomic’s innovative approach provides significant competitive advantages throughout the entire product value chain. To learn more, visit www.titomic.com.
ABOUT NUFORJ, LLC
nuForj is a Springfield, Massachusetts-based advanced manufacturing technologies and market insertion advisory boutique committed to helping industrial innovators realize competitive advantage from Industry 4.0 technologies. We leverage our team’s hundreds of years of combined experience to solve complex manufacturing challenges through technology-driven solutions, creating new sources of revenue while improving efficiency. We help convert IP into high-margin, sellable products, and we open up access to Industry 4.0 infrastructure and expertise across the entire ideation-to-commercialization value chain. Visit www.nuforj.com.
Ready to revolutionise your manufacturing?
Frequently asked questions
TKF costs significantly less than traditional manufacturing methods for the following reasons:
- It doesn’t need large-scale tooling (such as vacuum moulds) to produce parts. A simpler setup means reduced costs.
- It turns metal powder to part in just hours, by depositing the powder at supersonic speed to rapidly build up parts layer by layer – so there’s no need for casting or forging. Plus, the part you need is the part you make, saving time and materials.
- It keeps material costs down. For example, when we manufactured a 1.2m titanium ring, the ‘as built’ weight was 60kg while the final part weighed 56kg – representing a ‘buy to fly’ ratio of 1.08 with material costs of only A$3,000.
Our compact cold spray systems cost considerably less than traditional repair and resurfacing methods for the following reasons:
- You can resurface and refurbish parts in just minutes.
- Materials often cost less than $300.
- You no longer need to outsource repairs. For example, a shower floor manufacturer quoted $40,000 to ship a damaged resin transfer moulding tool overseas spent just $3,000 repairing it with Titomic’s D523 system – as well as saving months of downtime.
We’ve achieved typical density rates of 90-95% and over 99% when enhanced by post-processing.
If needed, it’s also possible to create less dense, more porous coatings for grip, abrasion, chemical processing and more through process optimisation, powder manipulation, and post-processing parameters.
Generally, you can achieve mechanical properties similar to casting and forging. While some parts may need to be processed with a heat treatment to make them more ductile, we can tailor process variables to meet your specific needs – a clear advantage compared to other methods.
It depends on what parts you need, as well as the mechanical properties the application requires. However, generally parts created with TKF will need some post-processing heat treatment.
Cold spray doesn’t require heat to melt the materials being sprayed. This is different to traditional metal spraying methods like welding or thermal spraying, which use heat to melt the material before it’s applied to a surface.
Instead, a high-pressure gas is used to accelerate tiny metal particles (which are usually less than 50 micrometres in size) to supersonic speeds. This creates heat through kinetic energy, when the particles collide with the surface of the object being sprayed.
Cold spray works by exploiting the kinetic energy of tiny metal particles. Low-to-high pressure gas is used to accelerate the particles (which are usually less than 50 micrometres in size) to supersonic speeds. These are then sprayed onto a surface where they compress and deform to create a cohesive bond.
This results in a strong, dense coating that can be used for a variety of applications – such as repairing damaged parts, improving the surface properties of a material, or creating new, complex shapes.
There are many metals that can be used in our cold spray systems. This includes aluminium, copper, nickel, titanium, stainless steel, Inconel, and more.
Since these all have different characteristics – such as strength, ductility, and resistance to corrosion – the chosen metals will depend on the application, as well as the properties needed for the final product.
Some metals may also be easier or more difficult to cold spray, depending on their melting point, ductility, and other factors.
What makes TKF so beneficial is that it can fuse dissimilar metals together. This means you can leverage the strengths of multiple metals in a single, monocoque part. For instance, you can fuse copper to titanium, nickel to cast iron, and much more.
Cold spray can be used on a variety of surfaces. This includes metals, ceramics, plastics, and composites.
The process is particularly useful for repairing worn or damaged metal parts, as it can restore the surface to its original shape and properties without causing distortion or weakening the material.
Our cold spray systems can also be used to add new features or properties to a surface, such as improved wear resistance, corrosion resistance, or thermal properties.
You can even use it to create new shapes or structures that would be difficult or impossible to achieve with traditional manufacturing methods.
- Aerospace: Repair and restore worn or damaged aircraft parts (such as engine blades, landing gear, and wing components), or add corrosion-resistant coatings to aircraft surfaces.
- Automotive: Repair and restore worn or damaged engine components (such as pistons, cylinder heads, and crankshafts), or add wear-resistant coatings to automotive parts.
- Marine: Repair and restore worn or damaged marine components (such as propellers, shafts, and rudders) or add corrosion-resistant coatings to marine structures.
- Oil & gas: Repair and restore corrosion and wear (such as shafts, bearings, piping, and valves).
- Electronics: Add conductive coatings to electronic components (such as circuit boards and antennas), as well as repair and restore electronic devices.
- Manufacturing: Create new shapes or features on metal parts (such as textured surfaces or complex geometries), or add wear-resistant coatings to industrial components (such as machine tools and moulds).