Often located in coastal areas, wind turbines are subject to extreme corrosion, leading to rusting and pitting. Once a part is damaged and deemed inoperable, parts often need to be replaced, leaving operators to foot the bill for the purchase, transportation, and installation of new parts.
The team at Fire Island Wind – a remote wind farm in Alaska run by GE Renewable Energy – needed repairs to a wind turbine heat exchanger. Replacing these heat exchangers is a logistical challenge, as they need to be drained, removed, and replaced, requiring hours of labor and costing up to $80,000.
Instead, the D523 was used to blast away the corroded material and then to coat the affected areas with less than $500 worth of aluminium. Over time, the aluminium forms an oxide layer, protecting the underlying surface from further corrosion for years to come.
The D523 uses a solid-state deposition method called cold spray, so it does not melt metals, and is able to fuse dissimilar metals together, including aluminium onto steel. Also, the repaired parts do not exceed 140 degrees Fahrenheit (60 °C), meaning heat exchangers can be repaired in-situ without draining, with no danger of deformation or affecting the metal’s grain structure. The system can also be used for repairs on ladder welds, broken teeth, gear boxes, shafts, and more.
Fast, nimble repairs for critical assets
The D523 was flown to Fire Island on a bush plane from Anchorage, Alaska. Once there, it was mounted on a light vehicle, complete with an air compressor and power generator. This enabled the portable and remote repair of these critical wind turbine structures.
Case study snapshot
What:
Wind turbine heat exchanger repair
Where:
Fire Island Wind, Alaska
How:
D523 low-pressure cold spray system with aluminium
Outcome:
Exchanger corrosion removed and coated in 2 hours, with corrosion protection to remain for years.
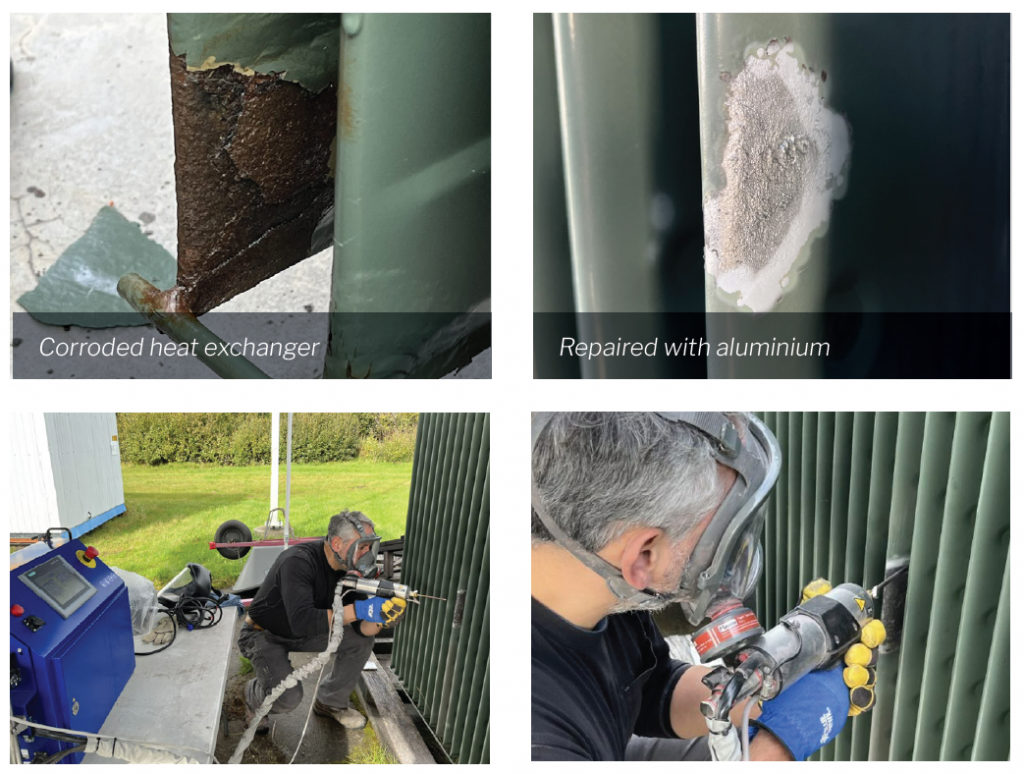