By Neil Matthews – Coatings & Repairs
Neil Matthews, a renowned expert in the field of Additive Metal Technologies (AMT), specifically Supersonic Particle Deposition (SPD) and Laser Additive Deposition (LAD), has received recognition for his research on the application of AMT in Australian Defence Force aircraft. He has been awarded with the Order of Australia commendation and brings a wealth of knowledge to Titomic.
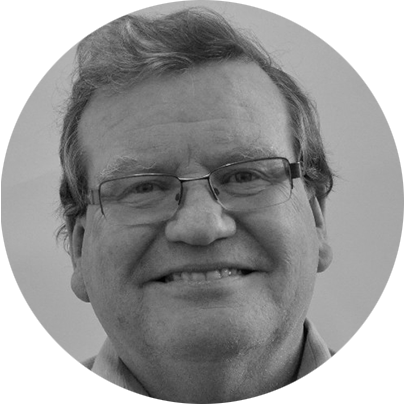
Cold spray is a solid-state deposition technology that has recently been applied as an additive process through a layered build to fabricate individual components, repair damaged components, and introduce coating solutions that enhance performance over existing coatings.
Unlike traditional additive technologies, cold spray utilises kinetic – rather than thermal – energy for metal deposition and therefore avoids residual stresses, oxidation, substrate material damage, and undesirable chemical reactions associated with thermal additive manufacturing processes.
Cold spray technology has demonstrated enhanced operational availability and reduction in lifecycle costs for the Australian Defence Force, such as the repair transmission cases within Royal Australian Navy‘s Seahawks, delivering significant downtime reduction and cost savings. For the RAAF F/A 18 fleet, cold spray technology delivered savings through the recovery of repairable items previously categorized as beyond physical/economic repair, and replacement spares.
The Australian Army is already evaluating in-field cold spray additive manufacturing to fabricate freestanding parts or to build features on existing components.
In a recent article2, the US Army has highlighted the effectiveness of cold spray technology, stating:
“Cold spray is an additive manufacturing technology that we’re using to repair parts” and “cold spray is used to repair many different materials”. “What is great about cold spray is that you can build up a surface and repair the part without putting a ton of heat on the part”.
Titomic is one of the pioneers in the development and application of cold spray technology and has now established a global presence delivering cold spray equipment, training, and solutions to customers in need. Titomic is also investing heavily in the development of economical ballistic protection using low-cost titanium powders. Development maturity is at a high level of confidence.
At Titomic, we’re convinced our current and evolving cold spray equipment and application solutions can deliver cost-effective, increased operational availability (uptime) while growing Australia’s sovereign capability in additive manufacture, additive repairs, and additive metal coatings. We also believe that our engagement can supplement the activities already undertaken by the Army in their engagement with cold spray additive manufacturing.
Now, we’re seeking to work with the Royal Australian Army to demonstrate, evaluate, and deliver cold spray sustainment solutions to end users through mechanisms such as the Defence Innovation Hub, Sovereign Capability Industry Priority (SCIP) programs, or direct projects.
The demonstration, evaluation, and delivery of Titomic’s cold spray technology – also known as Titomic Kinetic Fusion or TKF – offering an innovative and effective technology to assist the Australian Army to remain ready now and into the future.
Specific Opportunities
Titomic has developed unique equipment and applications solutions that could be readily tailored and implemented for increased operational availability in the following areas:
- Mobile cold spray technology solutions that can be incorporated on-site or at the damage location without component removal or disassembly. The intent is to restore form, fit, and function to allow operations to continue. Typical restoration would recover corrosion, wear, impact, and limited battle damage.
- Rapid additive manufacture of parts. Titomic is successfully generating low-cost, high-performing, large titanium shapes – up to 3 meters. Titomic’s demonstrably successful titanium cold spray now introduces an opportunity to produce lightweight, high-performing parts at costs similar to conventionally produced steel parts. This titanium cold spray technology is also demonstrating high levels of performance in ballistic trials. These two elements can also be combined for the manufacture of single-piece, monolithic, ballistically-rated titanium vehicle doors and panelling.
- New materials development to reduce in-service damage or degradation and replacement of existing, environmentally challenging chemical-based applications, such as electroplating or chrome/nickel coatings. In addition, cold spray technology allows new, better-performing material compositions to be deposited that cannot be generated through the thermal process (i.e., alloying). Titomic has demonstrated and validated several new cold-sprayed materials for sustainment.
As part of any of Titomic’s cold spray solutions, there are several elements that can be included depending on customer needs. These include the provision of equipment for standalone and “turnkey” operations, operator training, consumables, technical support, certified engineering solutions for customer acceptance, and incorporation endorsement.
References
- A message from the Chief of Army | Army.gov.au, LTGEN Rick Burr dated 31 January 2022
- Cold spray technology enhances Army 24 June 2021 | Article | The United States Army dated 31 March 2022
- The Australian AM technology promising to simplify sustainment – Australian Manufacturing Forum (aumanufacturing.com.au) dated 24 June 2021