A 3D measuring table is a highly precise, highly valuable casted part. If damaged, it can mean needing to recast the part, leading to extensive downtime. With welding ‘off the table’, recasting is often the only solution. Until now.
Cold spray is a no-heat metal deposition method that eliminates heat input. It utilises kinetic energy to mechanically bond metal powders and create thick, dense metal coatings and repairs.
The absence of heat offers several distinct benefits over traditional methods, such as welding. For example, there is zero risk of heat-related damage, such as cracking, warping, or changes to the metal’s grain structure. Additionally, parts do not need to be pre-heated, saving further time.
Another important aspect of using this no-heat process, is that it enables dissimilar metals to be fused together, such as nickel onto cast iron, aluminium onto steel, and so on.
In this case, Titomic used K714, a nickel alloy renowned for its repair capabilities, to quickly repair the casted 3D measuring table and return it to production in one day.
Challenges with casting repair
With low-value, or high-volume castings, the solution to handling defected parts is generally to smelt them and recast them. However, when dealing with extremely heavy or valuable castings, or castings which have already consumed valuable manufacturing time and capacity, it can be more efficient and more profitable to repair them.
Generally, this isn’t possible due to the heat generated by welding, which often introduces heat-affected zones and leads to parts being damaged further.
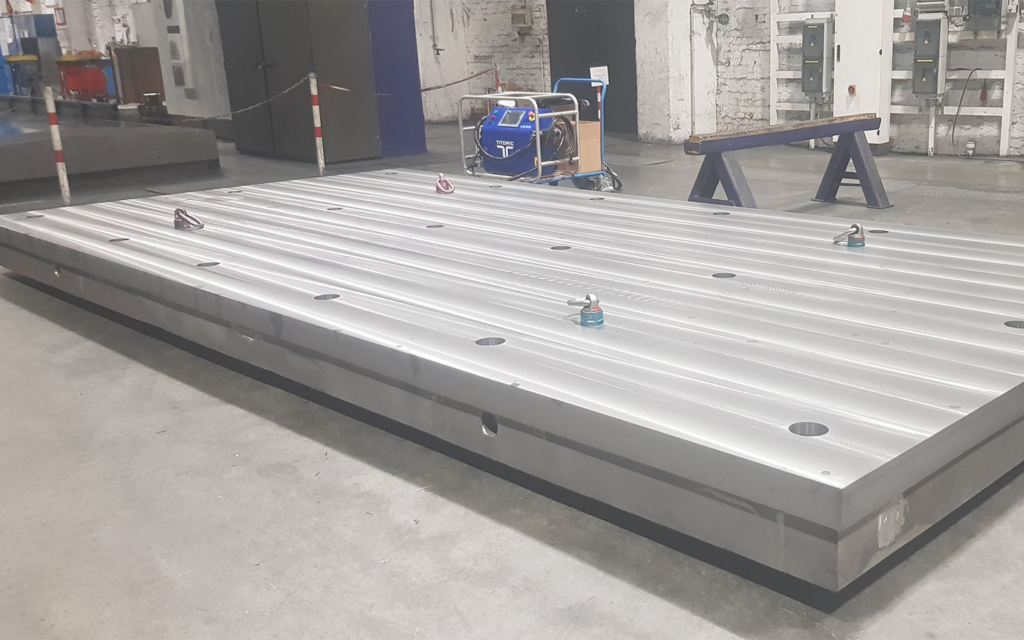
Cold spray: the most advanced way to repair castings.
Cold spray repair works by accelerating metal powder particles at supersonic speeds. As they impact a part’s surface, they ‘splatter’, forcing them to deform and mechanically bond to the surface and to each other.
The process of repairing with cold spray is incredibly simple. In this case, operators of the D523 opened up the defects with simple power tools. From there, the D523 was loaded with powdered K714 powder, a nickel alloy. Once the trigger is pulled, metal powder is deposited rapidly to fill defects, such as holes and scratches. Once done, the slight metal excess was removed to return the part to final tolerance.
Most importantly, cold spray maintains the density of casted parts, providing extremely dense coatings and metal depositions.
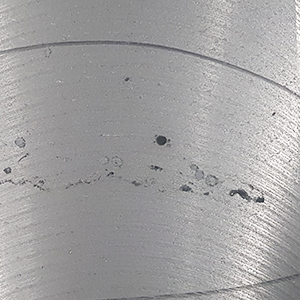
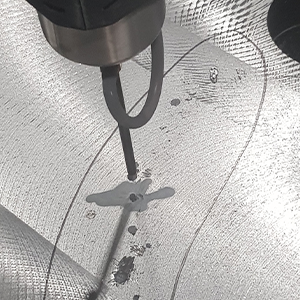
Damaged cast iron component, prior to repair.
The D523 cold spray system used to rapidly deposit nickel alloy to fill defects and restore geometry.
In-Depth Analysis: Density, Microstructure, and Material Composition in Cold Spray Repairs
The efficacy of Low-Pressure Cold Spray technology in repairing cast iron components is significantly influenced by the coating’s density, microstructure, and the composite materials used. The pioneering study by Koivuluoto, Kylmälahti, and Vuoristo (2011) provides critical insights into how these factors contribute to the successful restoration of casting defects.
Density
A cornerstone of LPCS technology’s success is its ability to achieve high-density coatings with minimal porosity. The study demonstrates that LPCS coatings on Fe52 steel substrates exhibit dense structures, which are pivotal for ensuring the mechanical integrity and longevity of repairs (Koivuluoto, Kylmälahti, & Vuoristo, 2011). This density is crucial for cast iron repairs, as it ensures that the repaired sections can withstand operational stresses without succumbing to premature wear or failure.
Microstructure
The microstructural analysis revealed that LPCS coatings possess a fine-grained, uniform microstructure. This is attributed to the rapid solidification of the particles upon impact, which prevents the growth of coarse grains. The study highlighted that the coatings’ microstructure plays a vital role in enhancing their mechanical properties, including hardness and bond strength, essential attributes for the durability of cast iron repairs (Koivuluoto et al., 2011).
Materials
Koivuluoto and colleagues (2011) investigated the use of zinc, aluminum, copper, and nickel, combined with alumina (Al2O3) particles, to create composite coatings. Each material was selected for its specific properties; zinc and aluminum for corrosion resistance through cathodic protection, and copper and nickel for their mechanical strength. The combination of these materials in the LPCS process allows for the tailoring of coating properties to meet specific repair requirements, such as enhancing the wear resistance or corrosion protection of the repaired cast iron component.
Case study snapshot
What:
3D Measuring Table, a component in a Coordinate Measuring Machine
Where:
Prominent manufacturer in Europe
How:
D523 low pressure cold spray system
Outcome:
Highly valuable casted part repaired in less than 8 hours, returned to production in one day.