Cold Spray for Engine Refurbishment
Titomic’s cold spray technology has emerged as a game-changer in the field of engine refurbishment, offering a sustainable and cost-effective solution for restoring critical engine components without the risks associated with traditional high-heat methods.
Recently, the D523 system was used to repair a corroded V-20 engine block, addressing worn Welsh plug seats and other damaged areas. This innovative process delivered high-quality results while minimising downtime, material waste, and operational costs.
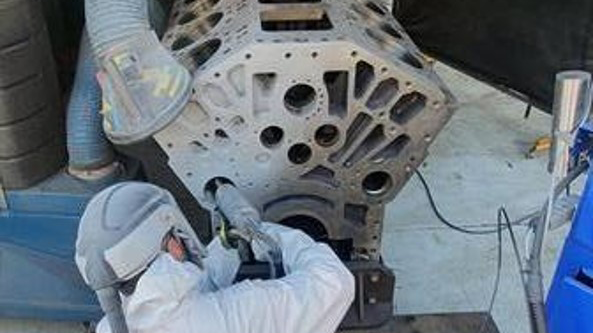
The Challenge
The refurbishment of large engine blocks, such as the V-20, traditionally relies on welding or thermal-based repairs to restore worn or corroded areas. These methods, however, often introduce heat-affected zones that weaken surrounding materials, cause warping, and compromise long-term performance. For this project, the corrosion in the Welsh plug seated area and adjacent surfaces required precision restoration without risking further damage or excessive downtime.
The Cold Spray Solution
Titomic’s D523 system is a low-pressure cold spray system, requring only single-phase power and compressed air to run. The system creates a supersonic air stream, which powders are fed into. As these powders collide with the part, they deform and mechanically bond together, creating dense, strong layers of metal.
In this case, the D523 was used to deposit Titomic’s K32 powder, a blend of aluminium and nickel, renowned for its durability and resistance to wear, corrosion, and heat.
Read on to see the steps Titomic took in detail to overcome this challenge.
Preparation:
The damaged areas were cleaned and prepped using a die grinder to remove oxides and sharp edges, followed by grit blasting to achieve the required surface finish.
Cold spray repair:
A 5–12mm layer of material was applied using the D523 system, avoiding the use of high heat to protect the engine block from thermal damage. As seen below the D523 system has effectively rebuilt corroded material. The welch plug seated area can now be post machined and engine block returned to service.
Benefits of Cold Spray Technology
- No Heat-Affected Zones Unlike traditional welding or brazing, cold spray operates at low temperatures, eliminating the risks of thermal distortion, warping, or metallurgical changes in the base material.
- Material Versatility The K-20-11 nickel alloy allowed for the precise restoration of the engine block, improving its wear resistance and extending its service life.
- Cost Efficiency By repairing rather than replacing the corroded engine block, the process significantly reduced material and labour costs.
- Minimal Downtime The rapid application and machining phases ensured the engine block was refurbished and returned to service faster than traditional methods.
The Outcome
The refurbished V-20 engine block was successfully restored, with the Welsh plug seated area rebuilt to its original specifications. The precision and quality of the repair demonstrated the suitability of cold spray technology for high-stakes applications, ensuring the engine block’s reliable performance without the delays and risks of conventional techniques.
Applications for Engine Refurbishment
Cold spray technology is increasingly adopted for a wide range of engine repair and refurbishment applications, including:
- Gasket mating surfaces
- Coolant galleries and Welsh plug seats
- Keyways and bearing bores
- Geometry repairs on engine blocks
- Sealing leaks and restoring structural integrity
Conclusion
Titomic’s cold spray technology redefines engine refurbishment by combining speed, precision, and material efficiency. For industries reliant on high-performance engines, such as aerospace, defence, and heavy machinery, cold spray offers an unmatched solution for reducing costs, minimising downtime, and extending the life of critical assets.
For more information on Titomic’s cold spray solutions, contact our team today.
Benefits of Cold Spray over Thermal Spray and Epoxies
- Enhanced Mechanical Strength and Abrasion Resistance
The cold spray process imparts superior hardness and toughness to the coated surface, making it ideal for areas subject to abrasion and impact. Epoxies, in contrast, lack this mechanical resilience.
- Minimal Surface Preparation
Cold spray requires less stringent surface preparation compared to epoxies and thermal spray, simplifying the application process and reducing time in repair scenarios.
- Geometry Restoration
Cold spray’s unique ability to rebuild corroded parts to their original dimensions is a game-changer for offshore maintenance. This capability ensures long-term functionality without the need for extensive replacements, unlike epoxies, which merely serve as a superficial layer.
- Material Compatibility
Cold spray supports a wide range of metals and alloys, allowing like-for-like repairs and compatibility with existing materials. Epoxies are limited to surface adhesion and often mismatch the base material properties.
- Superior Bond Strength and Corrosion Resistance
The metallurgical bond created by cold spray eliminates under-surface corrosion pathways, a common issue with epoxies that tend to delaminate over time.
- Environmentally Friendly
By eliminating the need for harsh solvents and chemicals, cold spray technology aligns with sustainability goals. This stands in contrast to epoxies, which involve environmentally harmful substances.
- Machinability and Weldability
Cold spray coatings can be machined and welded, enhancing their utility in repair applications. Epoxies lack this versatility, limiting their adaptability in complex offshore repairs. - Cold spray can be used for a broad range of applications, including for MRO within aerospace, defence, rail, and beyond. Check out how we repair train components here.
What is cold spray?
Cold spray is an advanced additive manufacturing technology that coats surfaces with strong layers of specialty metals – without ever melting them. In short, fine metal powder is acelerated to supersonic speed, and once these powders collide with the surface, they deform and mechanically bond together to form dense, strong layers of metal.
Want the full explanation on cold spray? Read further on how it works and comparisons between similar technologies.
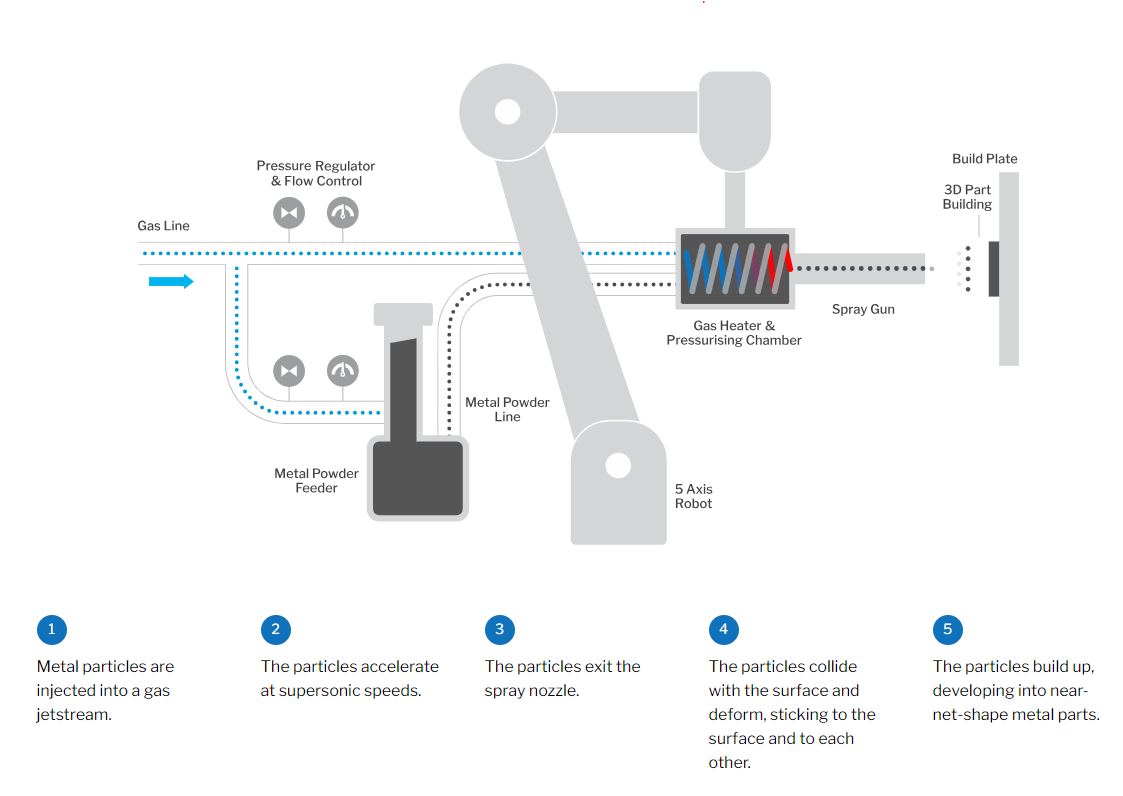