When engineering shop Mallee Machining Services was asked to repair a motor bearing housing suffering from wear, a lengthy and expensive sleeving process seemed to be the only option – until Titomic’s D523 low-pressure cold spray system turned things around.
Traditionally, restoring worn parts like a bearing housing requires resurfacing via sleeving. This is when a large cylindrical pipe billet is machined to the desired diameter and thickness, and then cooled so it can be forced inside the bearing. Not only is this a costly and time-consuming endeavour, it also results in around 80% of material being wasted, since the standardised billet has to be machined down to the right size.
For Mallee Machining Services, the project was anticipated to take hours and cost thousands of dollars – or more if the motor was welded and ended up cracking, or if the sleeve failed.
Low pressure, high savings
Using the D523 low-pressure cold spray system, we elected to resurface the cast-iron housing by applying a hard-wearing layer of nickel and filling the pitting and abrasion. Our team worked in tandem with Mallee, creating a jig to evenly coat the bearing and using rotational and lateral movement to apply the coating.
Since the D523 can spray metal in seconds, it took just one-and-a-half hours, 500 grams of nickel, and a mere $75 in material costs to bring the bearing housing back to working condition.
“The sleeving would have taken twice as long to complete, as cold spray halved the turnaround time,” says Mallee Machining Services founder, Anthony Riordan
Accelerating efficiency
Another benefit of the D523 is that minimal machining is needed to achieve financial tolerance. “It’s way more efficient, as we saved time by not requiring as many setups compared to sleeving,” Anthony said.
Case study snapshot
What:
Resurface and repair electrical motor bearing housing
Where:
Mallee Machining Services
How:
D523 low-pressure cold spray system with nickel
Outcome:
Bearing housing repaired in 1.5 hours for $75 in material – sleeving would have taken at least double the time and cost.
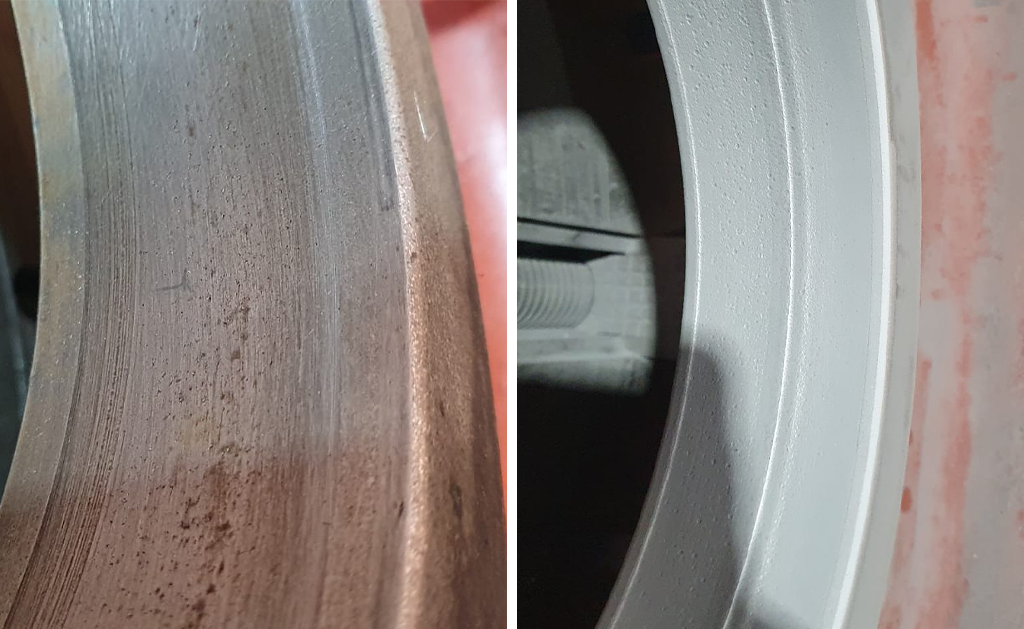