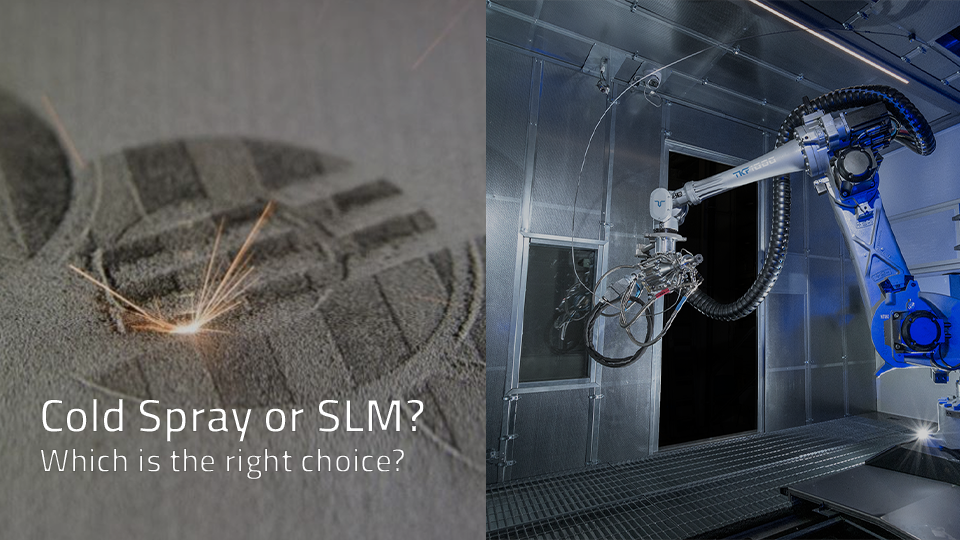
Selective Laser Melting (SLM) and Cold Spray are both quality methods for advanced manufacturing, but which one should you use for your manufacturing process? Each of them comes with different pros and cons in terms of:
- Design freedom.
- Strength.
- Material properties.
- Speed.
- Cost-effectiveness.
Selective Laser Melting (SLM):
High Precision with Heat
SLM is a common kind of additive manufacturing (AM). Most people opt for this method if they need something precise, as it’s able to produce quite complex geometries. You’d categorize this process as “powder bed fusion.” In short, metal powder is spread layer by layer on a powder bed and then the layers are selectively fused by a high-energy laser beam.
The laser that’s used during this process is intense, so it ends up melting each powder layer and creating a dense, solid structure once it’s cooled. The precision of the laser lets SLM build intricate designs – from internal channels to lattices – so you’d often see it used in the following industries, as they need precise and lightweight parts:
- Aerospace.
- Medical implants.
- Automotive.
Advantages of SLM
Why opt for SLM (Selective Laser Melting) over other manufacturing methods?
Design Flexibility and Precision
SLM enables the production of highly complex structures that would be impossible or cost-prohibitive with traditional manufacturing techniques. The selective melting of each powder layer also allows for an incredibly fine level of detail, down to the layer thickness of the metal powder, typically 20–100 microns.
Superior Mechanical Properties
By melting the metal powder fully, SLM creates parts that are dense and exhibit strong mechanical properties similar to wrought metal, making it an excellent choice for high-stress applications. The solidification during cooling enhances the material properties, often providing greater strength and fatigue resistance.
Material Variety
SLM is compatible with a wide range of metal powders, including:
- Titanium.
- Aluminum
- Stainless steel.
- Inconel.
This gives it a level of versatility that’s ideal for sectors that require different material properties. This flexibility in powder material only enhances its applicability across industries.
Challenges with SLM
Despite its advantages, SLM has some limitations. For instance, the process generates significant heat – this can lead to:
- Residual stress.
- Warping.
- The need for post-processing and heat treatment to relieve internal stresses.
You also need to perform SLM in a controlled environment that requires substantial energy due to the laser’s role. This can make it a more costly and slower process than some other additive manufacturing techniques, such as our next option.
Cold Spray: Rapid Production Without Melting
Another additive manufacturing method worth discussing is Cold Spray. This works similarly to SLM, except it operates on a fundamentally different principle – propelling metal powders at supersonic speeds onto a substrate rather than using heat to fuse powder particles. The particles deform and bond upon impact, creating a dense layer without melting.
This solid-state bonding process eliminates the risk of heat-induced changes, such as oxidation or thermal distortion, that are common with high-temperature methods like SLM. Cold Spray’s unique approach is highly advantageous for applications that require the following:
- Coatings.
- Repairs.
- The building of parts with high corrosion resistance and durability.
Advantages of Cold Spray
What makes Cold Spray such a special technique?
No Heat-Related Distortion
Cold Spray’s lack of thermal input is a significant benefit, particularly for components that cannot tolerate the microstructural changes caused by melting. Since the metal powders don’t melt, they retain their original mechanical properties, making Cold Spray suitable for high-strength alloys, corrosion-resistant coatings, and repairs where material integrity is critical.
Rapid Production
Cold Spray is a faster process than SLM, as it doesn’t require powder layer fusion. The process is scalable and can be applied across large surfaces or used to quickly build up thickness, making it an efficient choice for applications needing bulk material deposition, such as aerospace or automotive repairs.
Reduced Post-Processing
Unlike SLM, Cold Spray parts generally require minimal post-processing, as there is no need to mitigate residual stresses. This feature reduces the manufacturing time and cost, making Cold Spray particularly attractive for industrial applications with high production demands.
Challenges with Cold Spray
While Cold Spray has many benefits, it doesn’t offer the same level of detail as SLM. The process is less suitable for creating intricate geometries or complex internal structures. Additionally, Cold Spray bonding strength can vary depending on the type of powder material, and it may require additional measures to ensure durability in some applications.
Key Comparison: SLM vs. Cold Spray
How do these two methods compare?
Material Properties and Mechanical Strength
Both processes result in durable, high-strength parts, but SLM typically achieves a denser structure because of the complete melting and solidification process. However, Cold Spray parts, since they’re not subjected to melting, often have superior resistance to thermal distortion and retain the original mechanical properties of the powder material. Further, parts made with cold spray exhibit extremely strong mechanical properties after heat treatment, particularly hot isostatic pressing.
Production Speed and Scalability
Cold Spray is faster and more scalable than SLM, as it doesn’t rely on the layer-by-layer powder bed fusion. This makes Cold Spray ideal for large-scale production and repair work. SLM, while slower, offers unparalleled precision, which is critical for applications needing complex geometries and detailed structures.
Post-Processing Requirements
SLM parts often require extensive post-processing, including heat treatment, to reduce internal stresses caused by the laser’s high temperatures. Cold Spray generally avoids these post-processing steps, as its lack of thermal input eliminates residual stress concerns.
Cost and Energy Efficiency
SLM is more energy-intensive due to the laser energy required to melt the powder bed material fully. Cold Spray, by contrast, uses less energy and operates without a powder bed or laser beam, making it more cost-effective for larger, simpler parts or coating applications.
Which Method Is Best?
Choosing between SLM and Cold Spray largely depends on the specific application requirements:
For Precision Components with Complex Geometries
SLM is the preferred choice. Since it creates fine details and complex internal structures, you’d typically see it used for precision parts in the following sectors:
- Medical.
- Aerospace.
- High-performance automotive manufacturing.
For Large-Scale Parts and Rapid Repairs
Cold spray is more suitable for large, less intricate components and coating applications that require bulk material deposition without the risk of heat distortion. It is ideal for industries like aerospace maintenance and heavy machinery repair, where speed and material resilience are priorities.
When Thermal Stability and Original Material Properties Are Critical
Cold Spray’s cold-bonding process is beneficial for applications that require the metal powders to retain their initial properties, making it a great option for corrosion-resistant coatings and high-strength repairs.
If High Material Variety and Compatibility Are Needed
SLM offers more material options, as it works well with various metal powders that melt uniformly under laser energy. This versatility makes SLM adaptable for projects requiring specific metal properties or alloys.
Both SLM and Cold spray are valuable tools in the advanced manufacturing technology landscape, each with unique strengths and limitations. SLM’s selective laser melting process provides unmatched precision and density, which is ideal for complex designs and high-stress applications. Cold Spray offers rapid production and retains material properties without thermal distortion, making it well-suited for large parts, coatings, and repairs.